Cold Room Overview
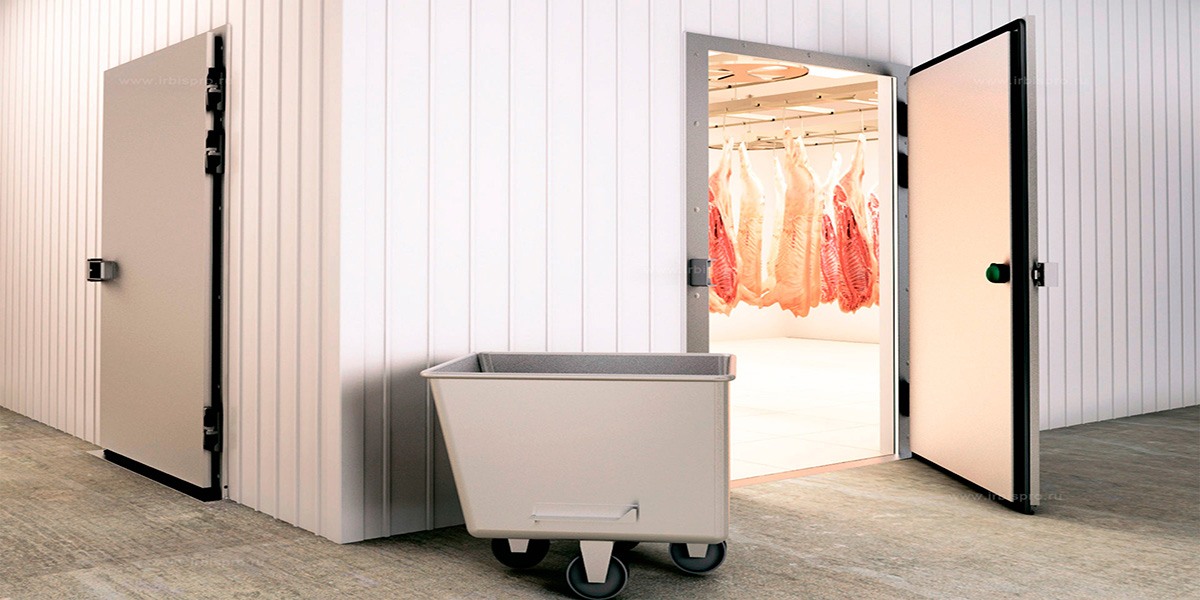
Found within the cold chain are cold storage facilities such as cold rooms. These facilities store or process both refrigerated and frozen products. They can be at the actual process facility or part of the distribution chain.
Compliance with hygiene and food safety regulations, but also energy regulations, is critical. Whether for a new installation or renovation, other parameters that must be considered when purchasing a cold room include ease of selection, refrigerant choice, installation options, reliability, maintenance, and operating costs.
We offers the widest portfolio of solutions for cold rooms to suit the diverse capacities, temperatures, and processes – for plug-in or remote installations, in small and larger sizes.
We offer contractor-friendly products & cold room solutions built with market leading expertise that are available everywhere and enable you to comply easily with regulations and save on installation and maintenance of walk-in refrigerators. Make the right choice for optimum protection of perishables, efficient operation and long lifespan.
Revacco is a trustworthy partner for the cold room storage industry, with an extensive range of refrigeration monitoring solutions, experience and know-how. Our solutions for reliable walk-in cold rooms are specially developed to cover the extensive range of commercial refrigeration applications within; food service (restaurants, catering), specialty retail (butchers, bakeries etc.), process cooling (lab, medical, fruit ripening etc.), convenience stores, discount stores, and pharmacies.
Cold Room Production
With the widest product portfolio for cold rooms, we offer a powerful combination of expertise and product options that will enhance your cold room design, and increase your bottom line.
Panels are produced in 2 types of insulation materials : Polyurethane (PUR) and Polyisocyanurate (PIR) in different insulation thicknesses. As external and internal surfaces of sandwich panel, painted galvanized, stainless steel, and Foodgrade or foodsafe materials can be used.
They are manufactured as polyester, plastisol, PVdf and food safe painted according to the needs of the Project. They can be manufactured in all RAL codes.
Interior and Exterior Surfaces ( Sheets )
The type and thickness of the metal used in the interior and exterior surfaces are determined according to the climate where the panel will be used, project's purpose and span distances.
Painted galvanized steel sheets are hot dip galvanized by
continuous process in accordance with EN 10143:2006 standards,
with 100-275 gr/m2 zinc-coated. Galvanized coating improves
corrosion resistance of the sheet. Due to its hardness, galvanized
sheet is resistant to impacts and abrasion.
On load bearing layers, galvanized sheet thickness should be
minimum 0,50mm.
Stainless steel is especially preferred in the interior and exterior surfaces of the Cold Storage panel for hygiene because of its acidic environmental durability and corrosion resistance. It is produced in different qualities. Products should be selected by taking only the mechanical and chemical values into consideration.316,304 and 430 grade stainless steel values in the following table are stated since they are the most frequently requested products on the market.
Paint
Polyester is the most simple and widely used topcoat paint among the paint types. It is widely used in interior and exterior surfaces. It is economical and it can be shaped easily. Since it has most appropriate cost, it can be supplied in all RAL codes. However, RAL9002 (white) is the standard
Foodgrade or foodsafe paints are food compatible topcoat paints used in cold stores of food sector. They are especially resistant to oils, acids, alkalies and chemicals. They are suitable for vapor resistant and cold storage areas. They are free of solvents and toxic substances. They are resistant to radiation, humidity and moisture; easy to clean and have a good corrosion resistance.
Insulation Core
Polyurethane (PUR) is rigid polyurethane foam formed by the mixture of two main components named as polyol and isocyanurate under special production conditions, with catalyst materials and under high pressure. It has a closed cell structure. Thereby, it can provide excellent thermal insulation. Polyurethane density must be between the range of 40 (± 2) kg/m3 so that the thermal insulation coefficient is at the desired value and for the carrier characteristics of the panel. It has high dimensional stability. Water absorption is not available, it floats on water. No bacteria grows inside. Its usage performance is good since it has high compressive strength. Usage temperature should be 70-80°C maximum. Maximum resistance temperature is 100-110°C. Above this temperature it loses its characteristics.
Polyisocyanurate (PIR) is formed as a result of the chemical reaction between the PMDI (polymeric methyl diphenyl isocyanate) or MDI and polyol. The amount of the mixture of MDI and polyol components differs polyisocyanurate from polyurethane. The amount of MDI used in PIR production and the amount of the flame retardant catalyst are higher. PIR is composed of isocyanurates chains which have higher chemical stability at high temperatures. PIR's flammability and smoke generation is very low compared to polyurethane. It creates excellent thermal insulation due to its closed cell structure. PIR should be used at maximum 80-90°C. Its maximum resistance temperature is 100-110°C. After this temperatures, it loses its function.
Condensing Units ( Outdoor Unit )
Line components and pressure controls for improved preservation and food safety.
Components:
-
Compressors
Fans
Filter Driers
-
Ball valves
-
Sight glasses
-
Pressure switches
-
Fan speed controllers
-
Condensers
Compressors
Designed highly efficiently for industrial refrigeration applications by leading brands like Bitzer, Dorin, Copeland, Danfoss, Tecumseh, etc. Various of types of American and European origin compressors are available at our disposal such as Hermetic, Semi-hermetics, Scroll, Screws for all applications.
Components for evaporators
Thermostatic and electric expansion valves, solenoid valves for energy efficiency and system reliability.
Benefits:
-
Help meet upcoming energy and environmental regulations
-
Available everywhere by your wholesaler
-
Reduction in electricity consumption
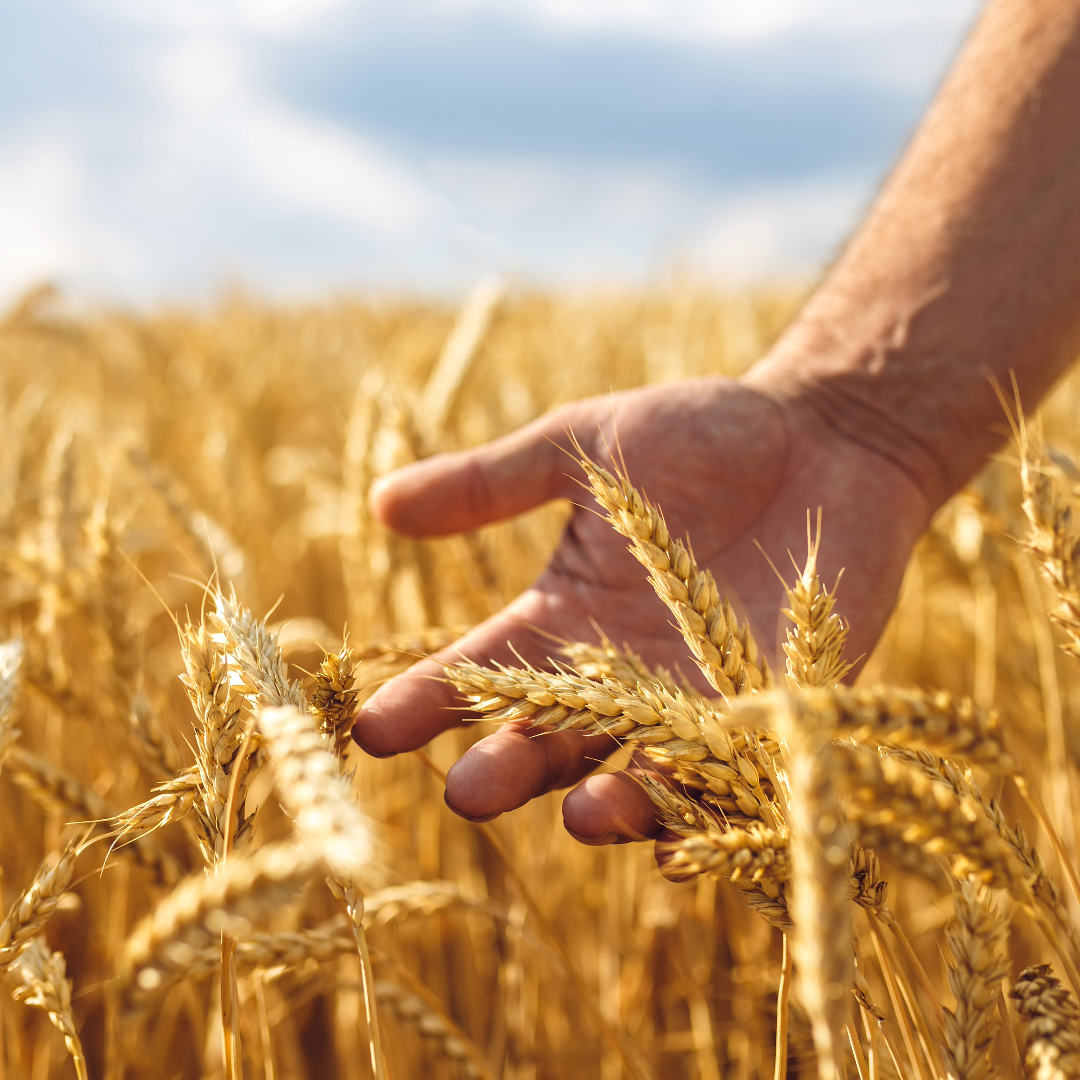
1/3 of all food produced in
the world is lost or wasted.
Food wastage reduction
is at the heart of global
and local international
programs. Cold chain
preservation to secure
food safety is not an option
but an obligation and is
another crucial aspect of
the global food demand.
Our solutions for
cold rooms help keep the
food fresh and safe for
consumption and therefore
contribute to reducing
food loss and waste.
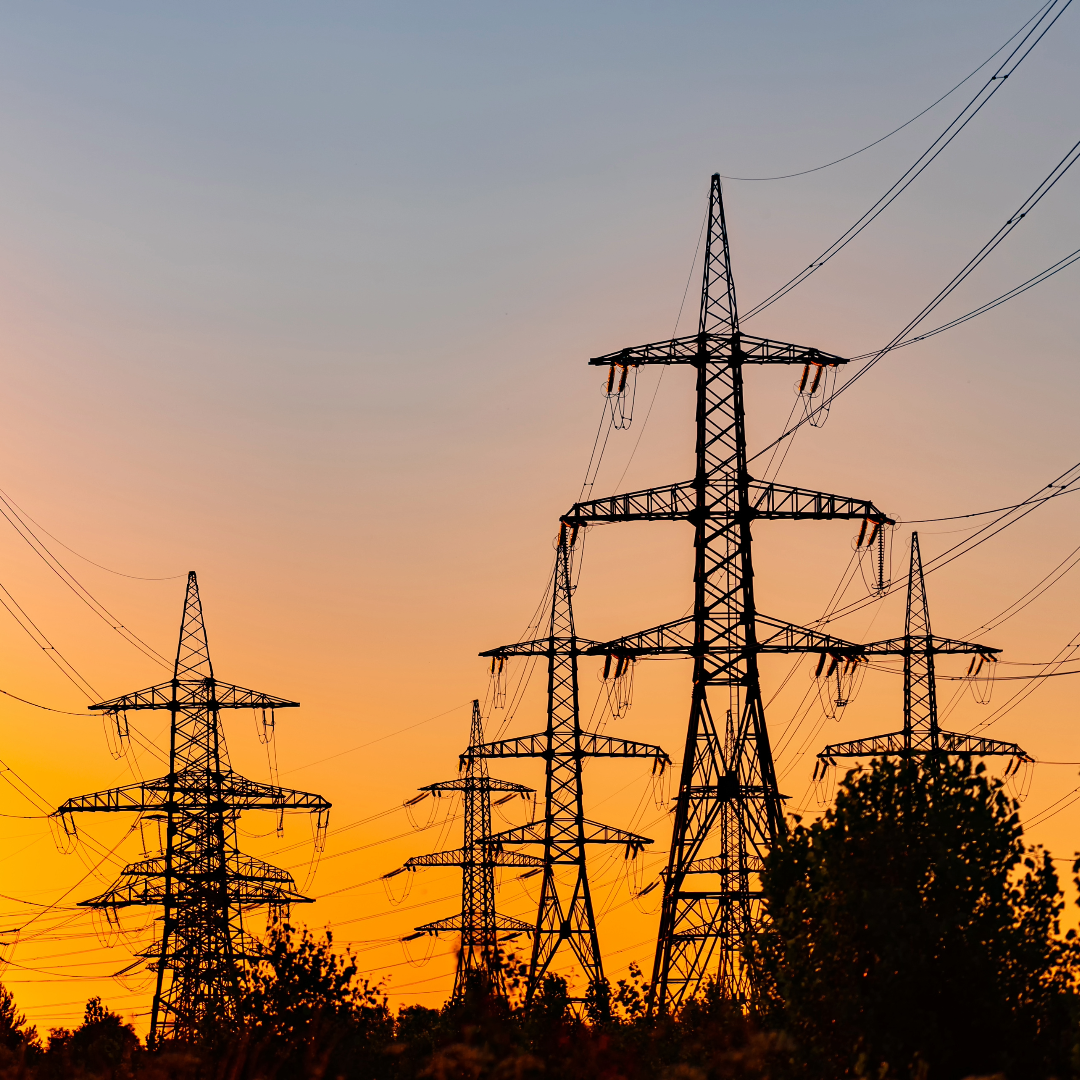
Cost and energy
production are among
the environmental
challenges of tomorrow
in many regions.This
is why we have been
working for a long time,
through our portfolio
of condensing units,
evaporator components,
drives, controllers, micro
channel heat exchangers,
and other components
to optimize cold room
lifetime, productivity and
monitoring.
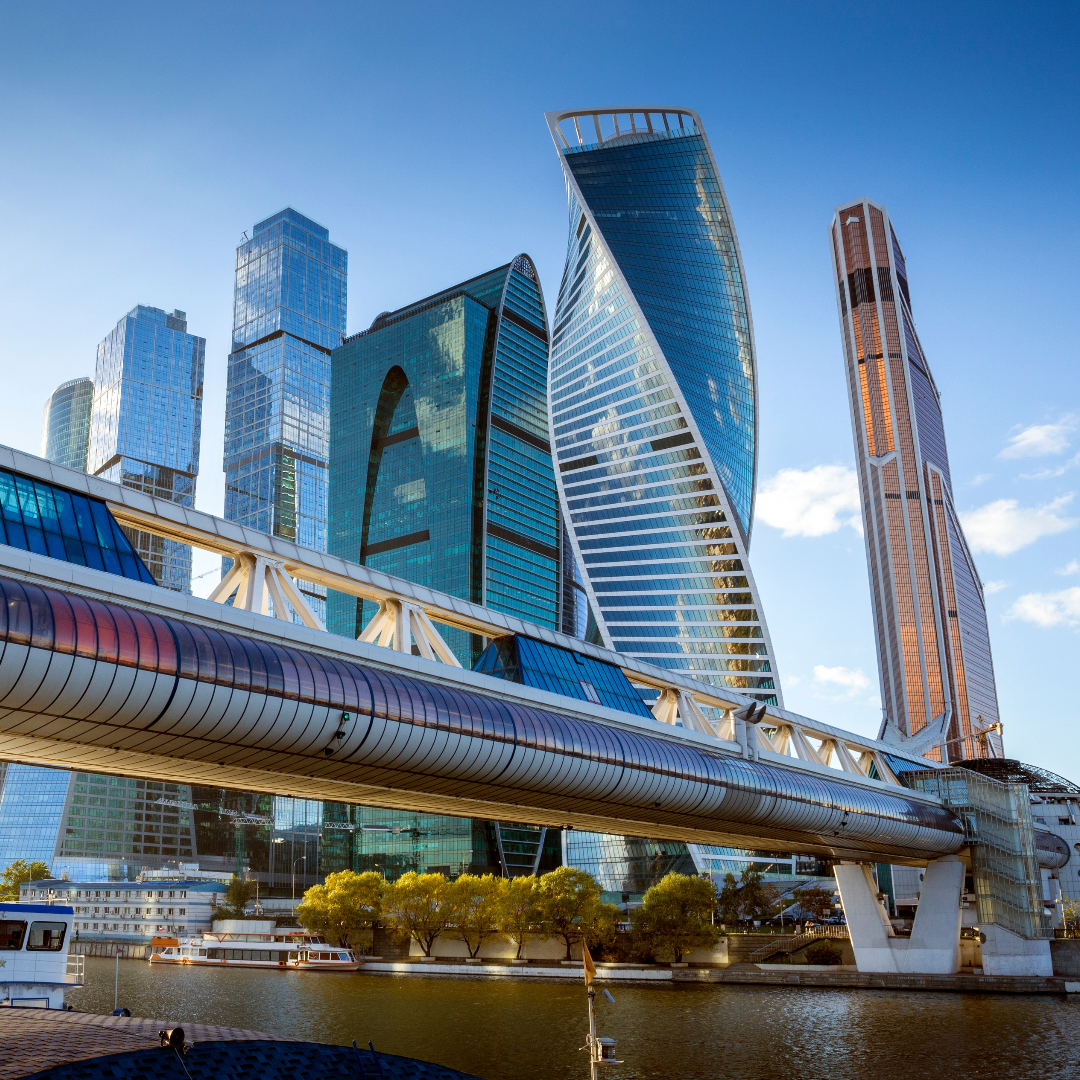
As the global population
continues to grow and
moves into cities, the need
for food storage equipment
increases. Revacco has a presence in in the international market,
selling in over 30 countries and partnering across a
wide distribution network in 5 major cities.
With our combined unmatched
application expertise, we
help meet these challenges
by building sustainable and
efficient cold rooms.
The revolution in the refrigeration market opens up new opportunities
Energy efficiency, urbanization, connectivity, electrification, low GWP
(Global Warming Potential) refrigerants, and food safety put high
pressure on cold room professionals such as installers, equipment
manufacturers, wholesalers, and users.
The demanding and continuously evolving regulatory landscape
represents a profitability risk for all the market players. It also
creates opportunities to rethink the ways of designing cold room
equipment for cleaner, safer and easier usage and to operate them in
a sustainable and efficient way.
Products that are easier to install, use, and maintain and are available
near you. Intuitive selection tools, local and global technical teams that
have the most extensive expertise in cold room components, are backed
up by strong support from distribution partners. We go beyond just
cold air as our products and solutions are evolving and anticipating new
regulations, while offering competitive and reliable solutions across the
entire cold room lifespan. Ultimately, we are enabling remote monitoring
and paving the way for future connectivity.